EN 10216-4 is the standard specification for seamless steel tubes for pressure purposes – Technical delivery conditions – Part 4: Non-alloy and alloy steel tubes with specified low temperature properties. P255QL, with a steel number of 1.0452, is one of the non-alloy quality steel grades designated by EN 10216-4. The EN 10216-4 P255QL seamless tubes are often used in services with a minimum temperature of -46°C.
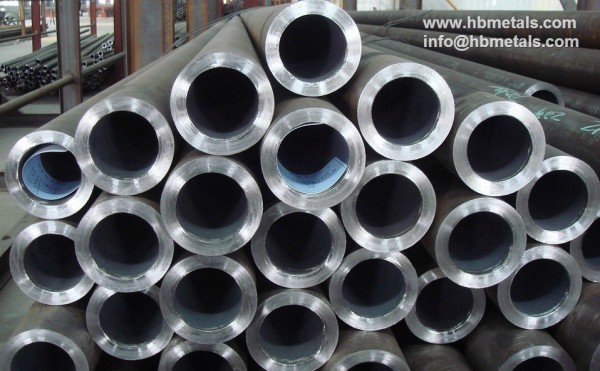
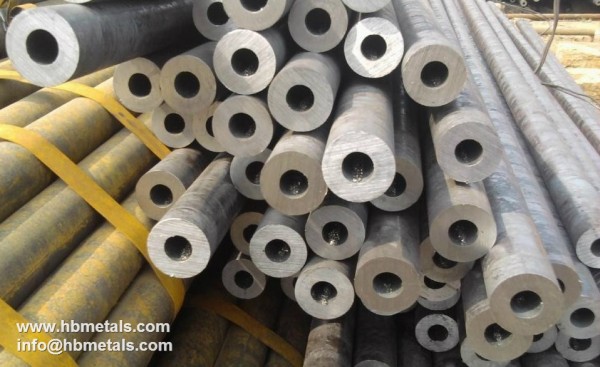
Chemical composition of EN 10216-4 P255QL / 1.0452
Element | Content by mass, % |
---|---|
Carbon (C) | ≤0.17 |
Silicon (Si) | ≤0.35 |
Manganese (Mn) | 0.40~1.20 |
Phosphorous (P) | ≤0.025 |
Sulfur (S) | ≤0.020 |
Chromium (Cr) | ≤0.30 |
Nickel (Ni) | ≤0.30 |
Molybdenum (Mo) | ≤0.08 |
Aluminium (Al) | ≥0.020 |
Copper (Cu) | ≤0.30 |
Niobium (Nb) | ≤0.010 |
Titanium (Ti) | ≤0.040 |
Vanadium (V) | ≤0.02 |
Mechanical properties of EN 10216-4 P255QL / 1.0452
Steel Name | Steel Number | Yield Strength, MPa | Tensile Strength, MPa | Elongation A Longitudinal, % | Elongation B Transverse, % |
---|---|---|---|---|---|
P255QL | 1.0452 | ≥255 | 360~490 | ≥23 | ≥21 |
Heat treatment conditions
For low-temperature purpose, EN 10216-4 P255QL shall be fully killed. The capital letter “P” stands for pressure purposes; “255” indicates the minimum yield strength of 255 MPa; “Q” indicates the heat treatment as quenching and tempering; “L” indicates the use for low-temperature purposes.
Usually the seamless tube or pipe of grade P255QL shall be quenched and tempered. The quenching temperature(hardening temperature) shall be at 890°C to 930°C while tempering temperature is ranging from 600°C to 680°C.